

Design variable bounds are also enlarged to +-25%. To challenge the optimization method, the problem size is expanded to have 30 design variables, 18 constraints and one objective function. This tutorial presents an ideal test case as it deals with a real nonlinear engineering problem, yet runs quickly, allowing us to test many scenarios. Performance of GRSM is tested on the design application covered in HyperStudy tutorial HS-4415: Optimization Study of a Landing Beam Using Excel. Having to choose from a list of specialized algorithms can be daunting
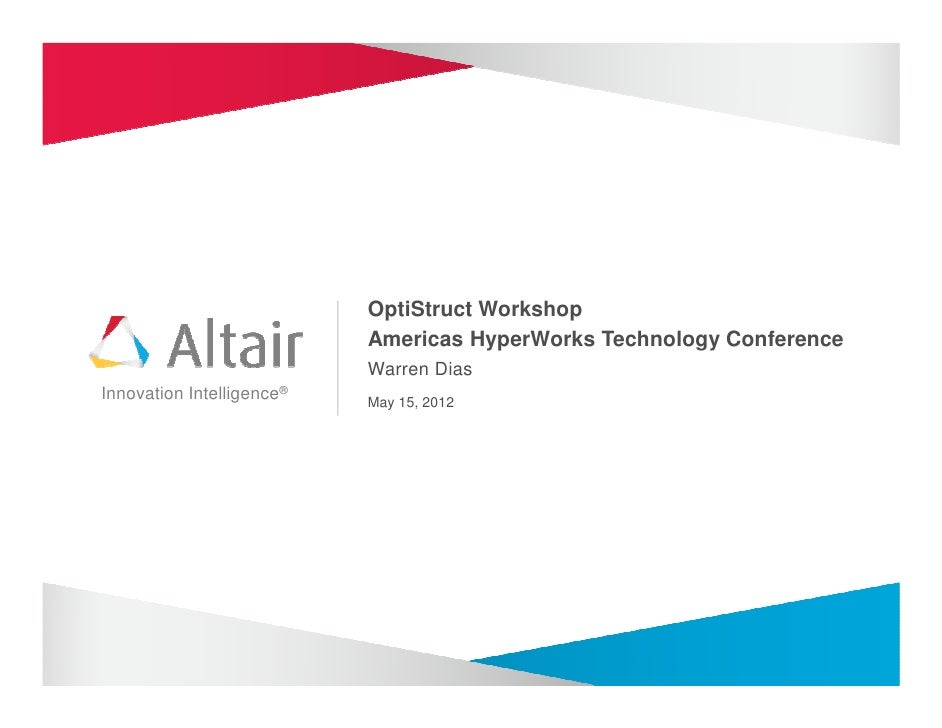
There are no other method parameters that must be fine-tuned. Aside from its wide range of applicability, GRSM’s most notable feature is that the user only needs to enter the number of designs they can afford to evaluate. GRSM works for both single and multi-objective optimization formulations, as well as handles both continuous and discrete variables. Furthermore, a number of concurrent evaluations may be dynamically controlled using the multi-execute option in HyperStudy. Note that these evaluations can be run in parallel to reduce the wall time of the study. GRSM repeats this loop until the user-defined number of designs is evaluated. The response surface is then updated, and the algorithm finds the optimum in this new surface. It then adds this design to the sample set, adding a number of new samples as well. The algorithm finds the optimum on this surface, and validates it with an exact simulation. Using these sample designs, it constructs a response surface.

GRSM first employs advanced strategies to sample the design space with a small number of designs regardless of the problem size. As a result, it is both efficient and the search is not limited to a local region.
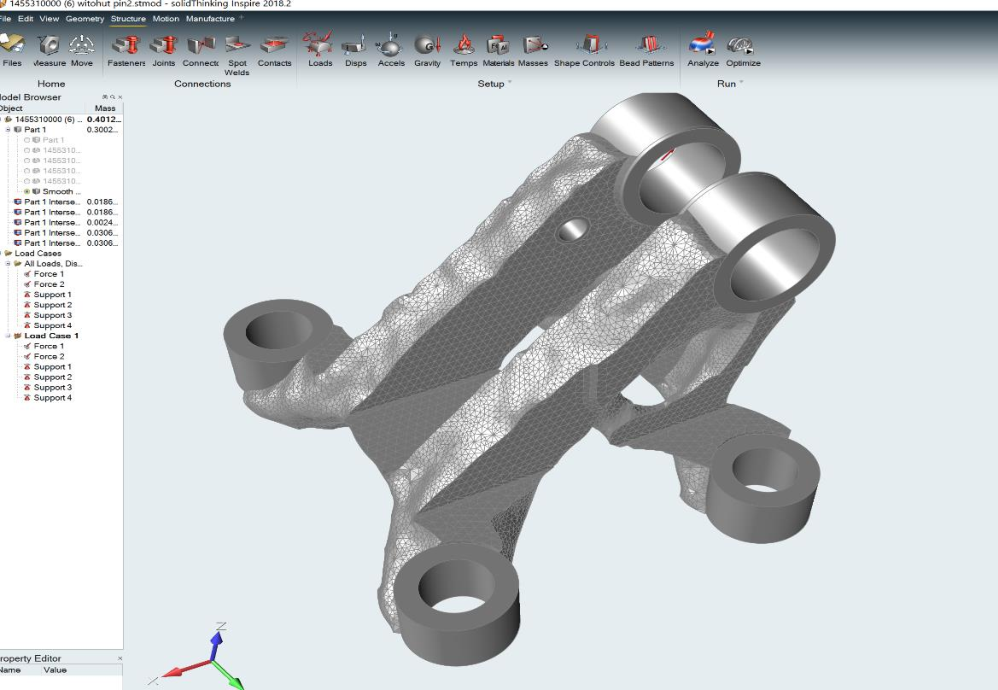
GRSM combines an adaptive response-surface-based optimization with global search. Global response surface method (GRSM) delivered with HyperStudy® 12.0 represents the culmination of this effort. With that ultimate goal in mind, the method development team at Altair has been working on an optimization method that requires minimal understanding of optimization theory, but still helps the engineer achieve his or her goal. The ultimate challenge was to find a one-click optimization that would work efficiently for a range of problems: local – global, single objective – multi objective, continuous – discrete, and linear – nonlinear. Optimization experts, despite happily finding jobs, were not necessarily content with this situation as it reduced the likelihood that optimization techniques were employed in engineering, thus not fully exploiting its potential. If there is only little room for improvement, then use a global search method but of course global search is expensive so first create a metamodel, which means running a space filling DOE, but which method to run? The questions and scenarios were plentiful with answers reflecting the experts’ personal opinion. If there is a computationally demanding simulation, do a space filling DOE and then create a metamodel and use this instead of the exact simulation. For a large number of design variables, do a screening Design of Experiments (DOE) first. Depending on the application, this exercise often became a full-blown project on its own. When mathematical optimization was first introduced to the engineering design world, an optimization expert typically sat with the design engineer to help them apply optimization techniques to their design applications retroactively. Fatma Koçer Business Development Director, Design Exploration
